What's Hot Runner
On this page, we will introduce the structure of hot runners and their advantages and disadvantages compared to cold runners.
Hot runner is a technology that produces only molded products by keeping the sprue and runner part for flowing resin in a molten state in injection molding of thermoplastic resins.
The hot runner system consists of a "nozzle" that supplies resin to the molded product, a "manifold" that branches the resin to each product, a heater that maintains the melting state of the resin, and a sensor for temperature control.
The hot runner uses a controller for temperature control to control the temperature by passing an electric current through the heater and maintain the melting state of the resin.
The molding method using a hot runner system is also called runnerless molding because it does not produce sprue runners.
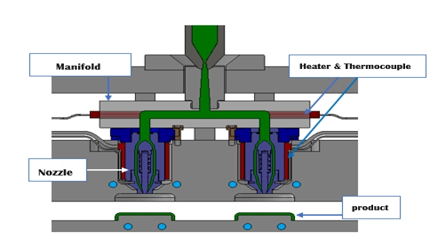
Differences from Cold Runner
The molding method in which the conventional runner is discharged is called the cold runner type.
In the cold runner type, the sprue and runner used to pour the resin into the molded part are also cooled in the mold and molded together with the product.
In other words, you're making things you don't need together
Compared to hot runners, cold runners do not require temperature-controlled equipment, so the initial cost is lower, but disposing of molded sprue runners is time-consuming and expensive.
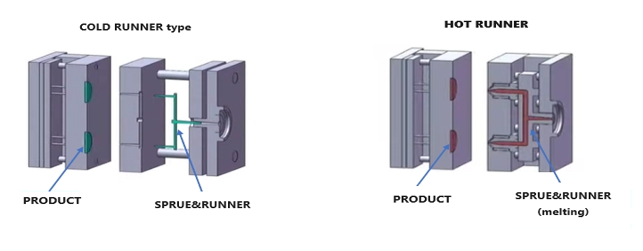
Advantages and Disadvantages
Hot runners have a big difference in molding method from cold runners, and there are advantages and disadvantages associated with it.
【Advantages】
There are no waste runners.
The hot runner keeps the sprue runner in a molten state, so there is no wasted runner
This reduces the time and expense of disposing of runners
Cycle times can be shortened
Since there is no need to cool the sprue runner, cooling time can be shortened.
The absence of a sprue runner minimizes the opening stroke of the mold, eliminates the need for runner retrieval time, and reduces overall cycle time.
Cost savings can be realized
The absence of waste runners reduces material costs and reduces the time and labor and equipment costs required to reuse waste sprues.
Shorter cycle times improve productivity and directly reduce costs
If the opening stroke of the mold can be reduced, it can be molded with a smaller molding machine, which can reduce electricity costs
Improved formability and expanded range of molding conditions
In the cold runner type, the temperature starts to drop from the sprue runner part, so the fluidity of the resin to the molded product is poor, and pressure loss is likely to occur.
The hot runner keeps the resin in a molten state until the gate, so the fluidity does not deteriorate and the pressure drop is minimized.
If the defect rate is reduced by these features, it will lead to cost reduction
【Disadvantages】
Requires initial implementation costs
Because of the need for hot runner components and a temperature control controller, the initial installation cost is higher than that of a cold runner.
Regular maintenance is required
Depending on the material to be molded, it is necessary to remove and clean the gases generated from the resin
Types of Hot Runners
Hot runners are classified into two types, "open gates" and "valve gates" according to the gate (= resin supply part to the product) structure of the nozzle.
As I will introduce next, there are differences in price and performance, so the selection is based on the molded product and budget that uses the hot runner.
【Open-Gate type】
The open gate type is a nozzle with the gate part always open.
Most of them have a heat storage tip attached to the tip to prevent the resin of the gate part from hardening, and although there are differences in these shapes, they are basically one type.
It is relatively inexpensive among hot runners, but since the gate is always open, it is a type that is prone to "stringing" and "dripping &falling" even if it is suppressed with a heat storage chip.
【Valve-Gate type】
The valve gate has a mechanism built into the nozzle to close the gate part, which completely prevents problems with "stringing" and "dripping&falling" from the gate.
Among valve mechanisms, there are multiple types depending on the structure, such as "electric valve", "hydraulic valve", "air valve", and "spring valve".
Regarding molding problems, please feel free to inquire at any time
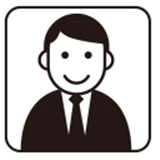
Hot runner technical consultation
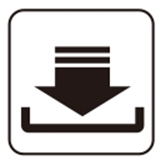
Download
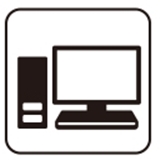
consult
contact us
If you have any questions, please click here to consult and look forward to your contact.
Service Hotline
0512-67086298